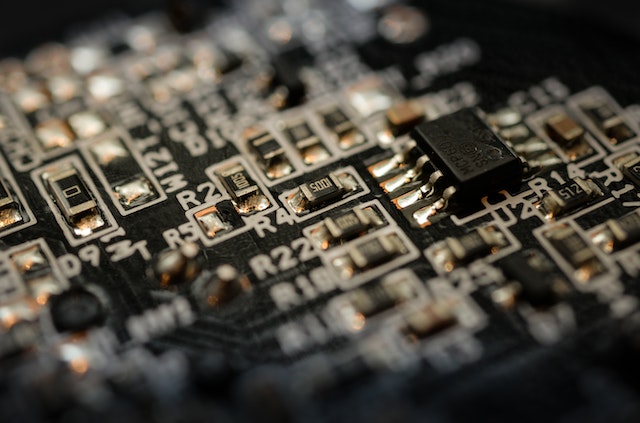
信頼性…これは、過剰に使用され、乱用されている用語です。
電子機器の分野では、「信頼性」とは機器の故障に関するものなので、次のような点に注目します。
- 製品を長持ちさせるためにどのように設計しますか?
- こうすると、「長い間」とは実際何を意味するのでしょうか?
- 信頼性をどのように測定し、目標を達成したかを確認するのでしょうか?
さあ、お茶を片手に、計算を最小限に抑えたワイルドな旅に出かけましょう。
信頼性とは何でしょうか?
まず、Wikipedia、数学、その他複雑なものには近づかないでください。信頼性はそれ自体が大きなエンジニアリング分野ですが、私たちの目的のためには、かなり単純化することができます。
明確にするために、いくつかのことを定義する必要があります。
故障: これは、機器が意図したとおりに動作していない、測定可能または検出可能な状態を意味します。電子機器の分野では、「おっと、魔法の煙が出てしまい、動作しなくなった」という例が簡単です。故障は煙ではありません (煙は症状です)。故障とは、機器が動作しなくなったことです。
(ペダンツコーナー: 故障には、断続的な動作、魔法の煙が出ないはんだ接合部の破損、その他意図しない動作のあらゆるケースが含まれます。)
障害: 障害とは、失敗の原因となった根本的な問題のことです。
障害は設計者にとって重要です。障害から根本的な障害を解明できれば、同じ障害が再び発生しないようにするために、設計変更など何らかの対策を講じることができます。
失敗とは、目に見えるもの、または測定できるものです。欠陥とは、失敗の原因となるものです。
MTBF : これは Mean Time Between Failures (平均故障間隔) の略語です。つまり、故障した機器のサンプルが十分に多い場合 (平均を計算できる場合)、これは特定の製品の故障間隔の平均時間 (つまり平均時間) です。MTBF は通常、時間単位で表されます。
故障率: これは 1/MTBF です。 すみません…計算が始まります。
例:
- MTBF が 1000 時間ということは、平均して、多数のサンプルのアイテムで 1000 時間ごとに故障が発生することを意味します。長く持続するものもあれば、それほど長く持続しないものもありますが、平均すると 1000 時間になります。
- 同じアイテムの故障率は 1/1000 = 1 時間あたり 0.001 故障になります。
(一般的に、MTBF は小さな数値に比べて理解しやすいです)。
FIT : もう 1 つの頭字語で、「Failures In Time」を意味します。これは 10 億時間あたりの故障率です。この故障率を 10 億倍します。
例:
- 上記の例を使用すると、故障率が 0.001 の場合、FIT は 10 億 * 0.001 = 10 万回の故障 (10 億時間または操作あたりの故障数) になります。
ほとんどの場合、故障率と FIT についてはあまり心配する必要がありません。MTBF に重点が置かれる傾向があります。故障率と FIT の説明を含める理由は、これらがある種の信頼性分析に必要となるためです。
バスタブ曲線: 特徴的な形状からこのように呼ばれています。
バスタブ曲線の簡単な説明:
- 製造上の欠陥などにより、製品の初期故障が発生する場合があります。
- その後、長期間にわたり通常の動作が続き、通常の摩耗や製品寿命中に発生する偶発的な事象によって一定かつ低い故障率が発生します。
- 製品寿命の終わりには、摩耗により故障率が上昇します。
メーカー保証は、初期故障に対処することを目的としています。通常、ほとんどすべての電子製品では、初期故障は最初の数百時間の動作で発生します。
信頼性を考慮した設計
高い信頼性(平均故障間隔が長い)を備えた電子機器の設計方法については膨大な理論がありますが、その多くはいくつかの単純なルールに簡略化できます。
- 電子機器が熱くならないように注意してください。熱は電子機器の敵です。
- 信頼できるメーカーの高品質な部品を使用してください。安いものが必ずしも良いとは限りません。
- 部品を定格より十分な余裕を持って稼働させます。ストレスを受けていないコンポーネントは長持ちします。
- 新しい設計をテストする – 電力使用量、自己発熱、温度上昇の影響を測定します。
- 電子部品の性質を理解する。
- 部品表を管理します – 工場代替は許可されません!
実用的な考慮事項:
電解コンデンサ
これらは、古くなるにつれて故障しやすくなることで有名です。
部品が定格電圧に近いほど、また高温で動作しているほど、故障の可能性が高くなります。5~10 年後に故障する多くの電子製品は、電解コンデンサを交換するだけで修復できます。
信頼性を高めるには、電解コンデンサが低温に保たれるようにし、定格「時間」がわかっている部品のみを選択し、常に十分な電圧マージンを確保するようにしてください。たとえば、12 V DC で動作する回路で使用する場合は、定格 12 V の部品を使用せず、代わりに定格 16 V または 35 V の部品を選択してください。コストは数セント高くなりますが、故障までの時間は 2 倍以上になる可能性があります。
さらに良いのは、電解コンデンサをまったく使用しないように設計を変更することです。
セラミックコンデンサ
これらは電圧の影響を受けることがよく知られています。つまり、直流電圧が印加されると静電容量値が低下します。静電容量の低下は大きくなる可能性があるため、通常の動作電圧よりも大幅に高い定格電圧を持つセラミック コンデンサを選択する必要があります。5 倍以上の電圧が望ましいです。
抵抗器
どのような種類の抵抗器も決して熱くなることはありません。
ただし、抵抗器は電力を消費する必要がある場合もあります。その場合は、少なくとも 2 倍の余裕があることを確認してください。抵抗器が 200 mW を消費する必要がある場合は、1/2 W 定格の部品を使用してください。
半導体(トランジスタ、MOSFET、ダイオードなど)
他のすべてと同様に、これらが定格に近い値で実行されないように注意してください。
多くの半導体部品は、高電流を流す必要があります。たとえば、半導体スイッチ、調光器に使用される MOSFET などです。これらの部品を使用する場合は、加熱と温度上昇の影響を確認し、これを安全限度内に抑えてください。MOSFET やその他の部品には、メーカーから提供される「安全動作」グラフがあります。すべての動作モードで、デバイスがその安全動作領域内で十分使用されるようにしてください。さらに、ベンチ プロトタイプだけでなく、実際の製品で全体的な加熱を確認してください。
可能な限り、定格に余裕を持たせてください。たとえば、トランジスタが 250 mA を流す必要がある場合は、500 mA を処理できる部品を使用します。これによりコストは増加しますが、製品の堅牢性が向上し、早期故障の可能性が低くなります。
ノブ、ダイヤル、そして「細かい部品」
顧客の管理に必要な場合を除き、このような調整や調整可能なコンポーネントは、衝撃や衝突を受けやすく、温度に依存する影響が出ることがあります。
可能であれば、そのようなコンポーネントは避ける必要があります。
はんだ接合部とコネクタ
著者が信頼性を研究していた当時、これら 2 つの部品は電子機器の故障の典型でした。電子機器の最も悪い部品は、はんだ接合部とコネクタです。
残念ながら、はんだ接合部はすべての電子機器をつなぎ合わせる接着剤であり、設計上はそれをなくすのは現実的ではありません。私たちが期待できるのは、製造元が IPC 標準に準拠した十分に特性化されたプロセスを使用し、検査プロセスを使用することだけです。
検査プロセスもコストを追加します。
コネクタは電子機器の故障の原因になることもよく知られています。可能な限り、コネクタは使用しないでください。コネクタを使用する必要がある場合は、次の点を考慮する必要があります。
- コネクタピンを通過する電流はどれくらいですか?
- 予備ピンまたは冗長ピンが必要ですか?
- そしておそらく最も重要なのは、コネクタの金メッキを慎重に検討することです。
異なる金属が接合するコネクタ (金プラグ/錫ソケット) は絶対に使用しないでください。これらは常に動作の信頼性を低下させます。
金メッキでも注意が必要です。最も安価なフラッシュゴールドは薄すぎて役に立たない場合があります。そしてもちろん、使用される金の量が多いほど、コネクタは高価になります。
信頼性設計の要約:既知の問題のあるコンポーネントを避け、既知の品質の部品を使用し、定格から余裕を持たせ、コネクタに金を使用し、はんだ付けプロセスを検査します。
基本的に、コストを追加する一連のもの。
製造バーンイン
場合によっては、製品は製造工場内で稼働することもあります。稼働時間は数分、数時間、またはそれ以上になることがあります。稼働時には、リレーや調光器で大きな負荷を制御するなど、ある程度のストレスがかかることがよくあります。
バーンインの目的は、早期故障を起こした製品(バスタブ曲線を参照)を見つけ、製品が顧客の手に渡る前にそれらの故障に対処することです。
バーンインもコストを追加します。
信頼性予測
信頼性を予測することは可能ですか? たとえば、新製品の MTBF を計算してみることはできますか?
すべての分野と同様に、信頼性エンジニアは、はい、これは可能だと言うでしょう。
1960 年代から 1990 年代頃まで、防衛および通信企業は信頼性の分析と予測に多大な労力を費やしてきました。その結果、品質の異なるさまざまな予測方法が生まれました。
これらの予測方法の基礎の多くは現在では時代遅れになっており、多くの現代の電子部品は予測方法が考案された当時に使用されていた部品よりも優れた特性を備えています。
それでも、利用可能な予測方法は、私たちが利用できる唯一の広く理解され、アクセス可能なツールであるため、それらを使用するだけでなく、その弱点も理解する必要があります。これらのツールを使用した予測はおそらく控えめです。つまり、実際には、実際の MTBF はより大きくなると予想されます。
おそらく最もよく知られている予測方法は、軍事(およびその他すべて)の電子機器で一般的に使用されている MIL-HDBK-217F と、通信で一般的に使用されている Bellcore/Telcordia です。
これらの規格と関連ソフトウェアのモデリング、使用、適用は複雑で、通常は専門家の領域です。MIL-HDBK-217F の場合、簡略化された「部品数」方式により、ほとんどの設計エンジニアが実行できる非常に簡単な推定が可能になります。この方法では、上記の信頼性設計セクションは考慮されないため、たとえば、コンポーネントにストレスがかからないようにすることは、結果に影響しません。
信頼性の分析と予測に使用されるソフトウェア パッケージには、RelCalcなどさまざまなものがあります。
部品カウント法に基づいて MTBF を推定したい設計エンジニア向けに、Reliability Analytics Toolkit Web サイトにオンライン計算機が用意されています。
信頼性の測定
簡単でしょう?失敗を数えてください。
実は、そんなに簡単なことではありません。
すべての失敗を数えることはできない
信頼性は物理的な事柄、および製造された製品の固有の動作に関するものであるため、一部の障害はカウントしてはなりません。
数えるのはダメです:
- ユーザーまたはインストーラーのエラーまたは損傷。
- 製造業者が間違った部品を使用していること
- 期待どおりに機能しないソフトウェアまたはファームウェア。
これらは残念なことであり、修正が必要になる可能性がありますが、MTBF の計算にカウントされる障害ではありません。
他にも、望ましくない可能性があるがカウントされない製品の動作があります。上記は無視しなければならない主なものです。
なぜ?
- 設置者が端子に配線を誤って取り付けたり、製品を落として壊したりすると、設計上の改善点が明らかになる場合がありますが、経年劣化や摩耗を示すものではありません。
- 製造業者が間違った部品を使用すると、プロセス障害となり、製造業者が修正する必要があります。
- ソフトウェアやファームウェアは、時間の経過とともに劣化することはありません。指定された動作や期待された動作を実行しない場合があります。これには、奇妙で断続的な動作 (タイミングに関連するいわゆる「ハイゼンバグ」) が含まれます。
信頼性テストを行う際には、測定をいつ再開するかに関連するその他の複雑な問題もありますが、これらは信頼性の専門家が扱う問題であり、簡単にするために無視することができます。
信頼性を測定する理由
信頼性を測定し、製品の MTBF を推定する主な理由は 2 つあります。
- 測定されたデータは予測よりも優れています。したがって、製品の実際の使用時間に基づく MTBF 数値は予測よりも優れています。
- 共通の要因や傾向が見られ、設計の改善が可能になります。
信頼性測定の実践的側面
信頼性を測定するには、組織として次の 2 つの重要な考慮事項が必要です。
- 不良品は返品、分析し、根本的な欠陥を記録する必要があります。
- これは長期的な取り組みです。
これらを詳しく説明すると、
市場および設置寿命が長い (5 ~ 10 年) 製品を製造する場合、実際の故障を測定する唯一の方法は、故障した製品を返品してもらうことです。返品されなければ、意味のある情報を収集することはできません。
価値の低い製品の場合、たとえば卸売業者が、廃棄して交換した不良品の数を毎月または四半期ごとに記録することは許容される可能性があります。分析はなく、根本的な欠陥に関する情報もないため、大まかな MTBF 数を判断するために利用できる情報はごくわずかですが、詳細な情報は利用できません。
それぞれの障害を分析することによってのみ、設計の改善に役立つ共通の根本原因を特定することが可能になります。
したがって、製品の故障を真剣に分析するには、サプライヤーが故障した製品を受け取り、故障を分析し、一般的な欠陥を見つけて、それに対して何らかの対策を講じる必要があります。これらはすべて、継続的な製品改善の長期的な視点を必要とする費用です。